You want to create conductivity on non-conductive objects? Discover our professional conductive varnishes now!
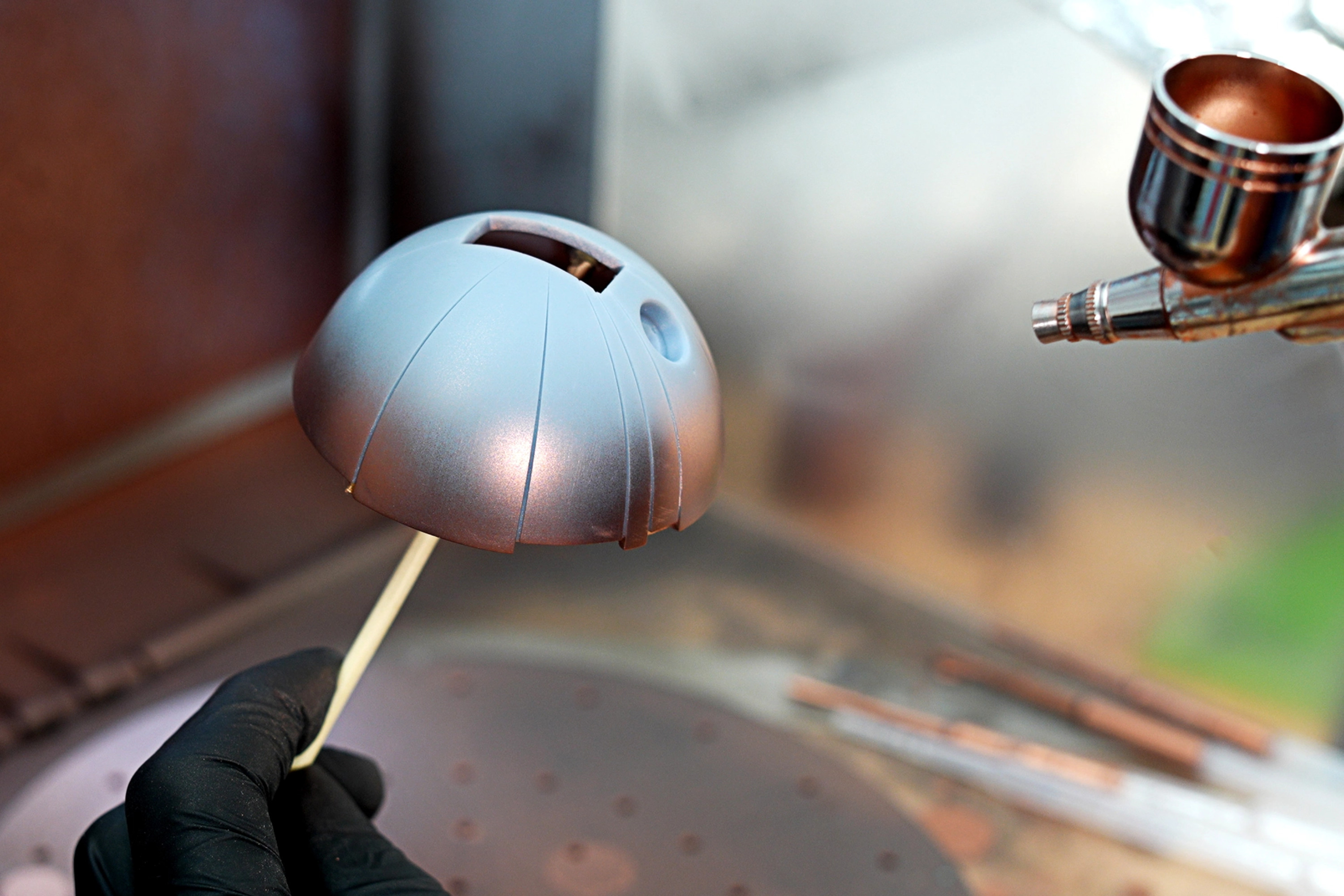
Copper conductive varnish
Silver conductive varnish
Valuable Tips
- Always ensure that the surface of the workpiece is clean, degreased and roughened to increase the adhesion of the lacquers.
- For mirror-like results, we recommend careful sanding with sandpaper from rough to fine and a light polish before all steps.
- Make sure that you can paint all parts of the object without any problems. Only when the surface is painted completely metal can be deposited later.
- Allow the conductive lacquer to dry sufficiently before carrying out further electroplating steps.
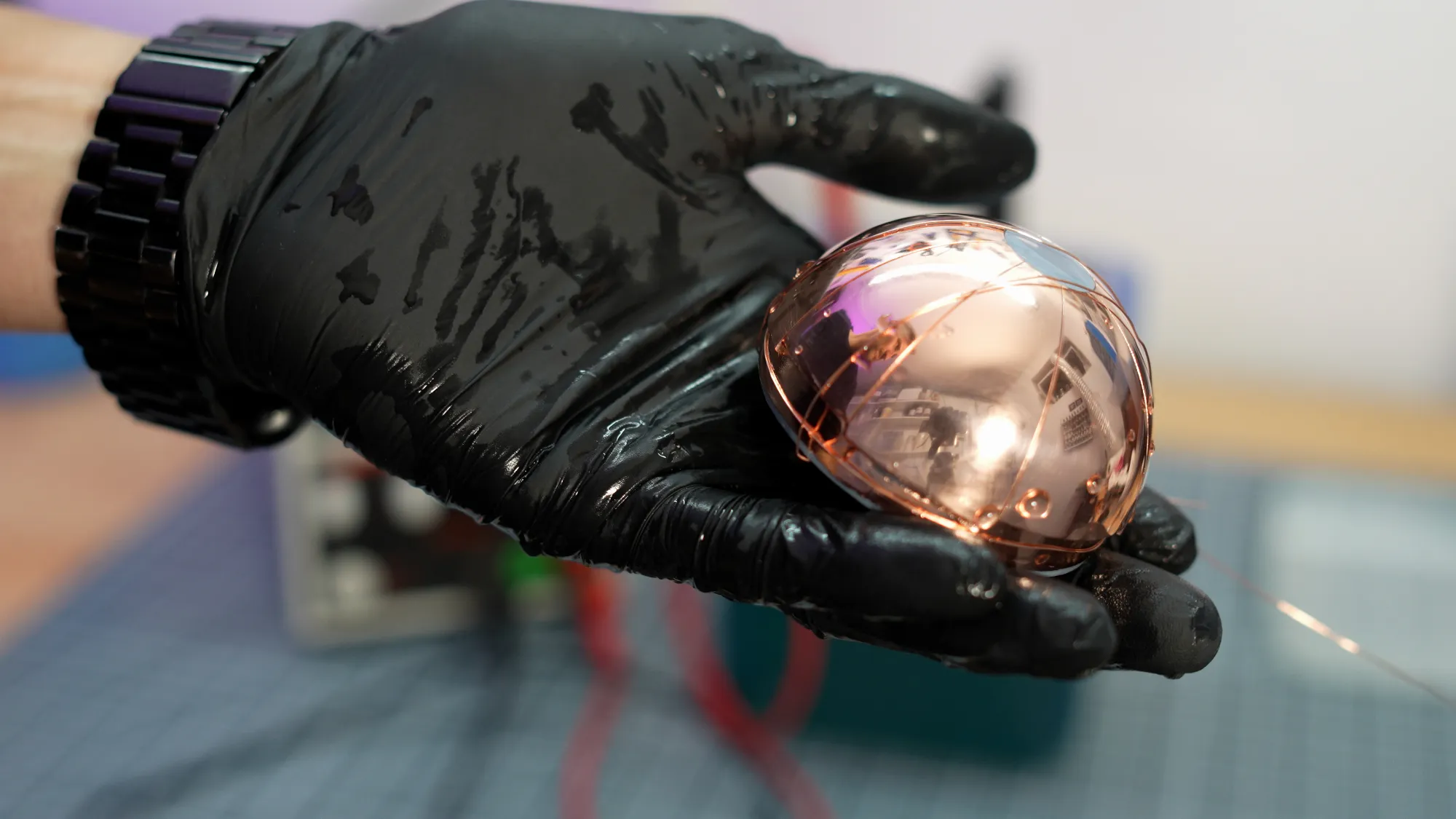
Frequently asked questions
Yes, this is possible with the help of our conductive copper varnish. The object is sprayed or brushed with copper conductive paint or copper conductive lacquer spray, which first creates a metallic layer. The object is then given its final conductivity in a galvanic bath with acidic bright copper electrolyte. This creates a continuous, conductive copper layer that can then be further treated like any other copper layer, e.g. by silver plating.
Rust Piranha can normally be painted over or treated further. However, please check on an inconspicuous spot whether the rust converter is compatible with your paint colour.
Our products for electroless silver plating only deposit on copper and brass as a base, as the products can only deposit silver with these materials. Accordingly, the products for electroless silver plating can NOT be deposited on silver. If copper or brass are coated, a thin silver layer of 200 - 300 nm is produced, which is intended for decorative purposes only. If you want a thicker silver layer on your object, the only process left is electroplating!
No, unfortunately that is not possible with these products.
In principle, it is possible to gold-plate some aluminium alloys with the Gold Star, but so far this only works with a few compositions. The success of the application can therefore not be guaranteed for all aluminium alloys.
The zinc object must be clean and free of residues such as dirt, oil or particles. The object is then degreased, e.g. with the TIFOO Galvano Degreaser. Depending on the size, the object is immersed in the yellow chromate for a few minutes. 3 minutes is a good guideline.